Kernsanierung
In der Rubrik Stories ist nachzulesen, wie die HB3 Anfang 2021 zu mir kommt. Bereits beim Kauf ist klar, dies wird definitiv ein zeitaufwendiges Großprojekt. Beim Zerlegen zeigt sich, dass die Bimota als reines Fahrgerät genutzt und bei der Wartung nur das Nötigste gemacht wurde. Pflege stand offensichtlich gar nicht auf dem Programm. Je mehr ich zerlege und reinige, desto mehr kommt ans Tageslicht. Es ist schon erstaunlich wie wenig Interesse manche Besitzer an ihren Raritäten zeigen. Eine HB3 hat 1984 deutlich mehr als ein Golf II GTI gekostet und es wurden nur 101 Exemplare gebaut, von denen heute deutlich weniger existieren und zudem über die ganze Welt verteilt sind.
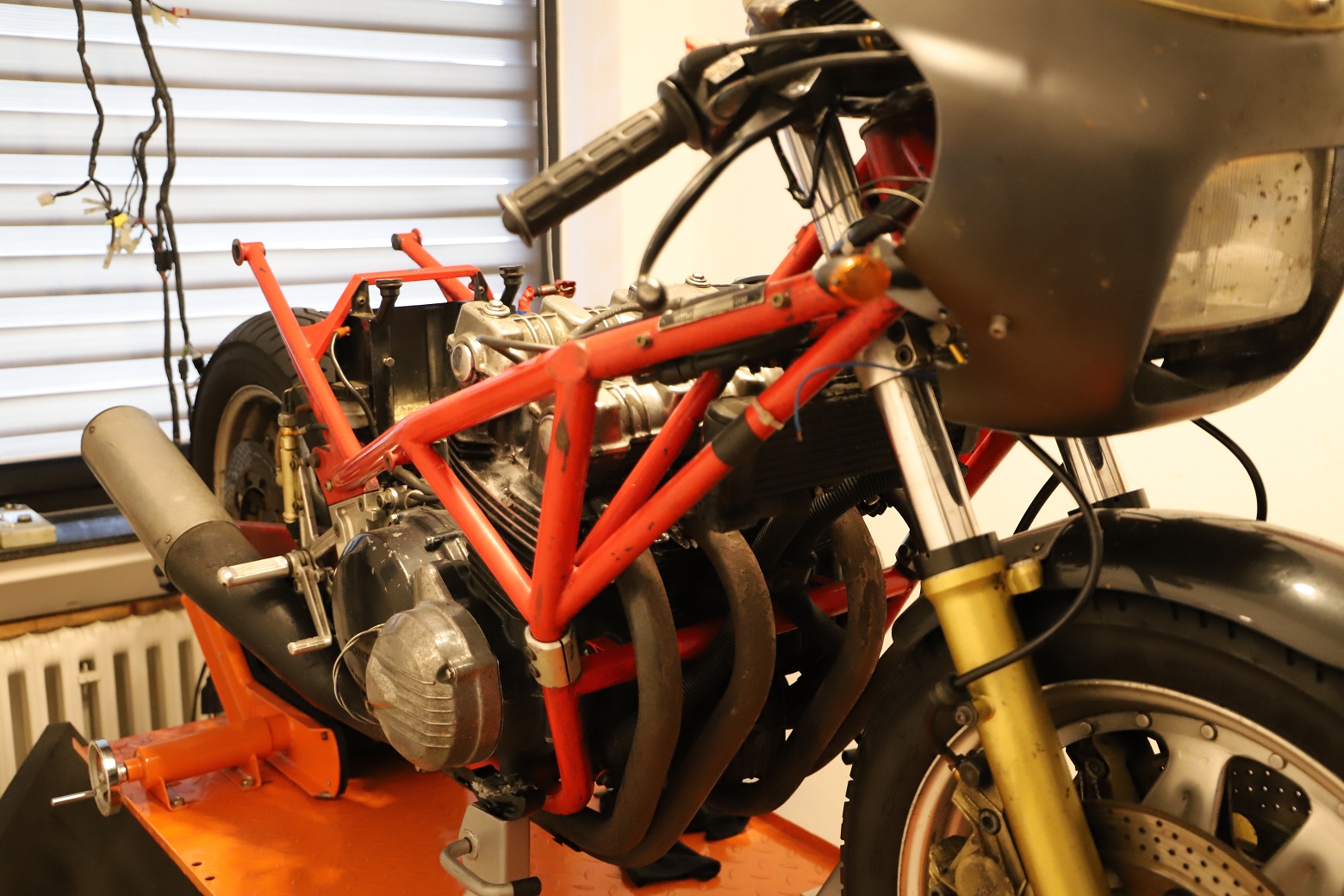
Im folgenden eine kleine Galerie, die den Restaurierungsaufwand einigermaßen erahnen lässt. Ausgelaufene Säure hat dem Batteriekasten zugesetzt. Der ist aber noch zu retten. Nicht mehr zu retten sind die Endschalldämpfer. Unter den genieteten Alublenden finden sich die vom Rost durchfressenen, originalen Endtöpfe, allerdings ohne Innenleben.
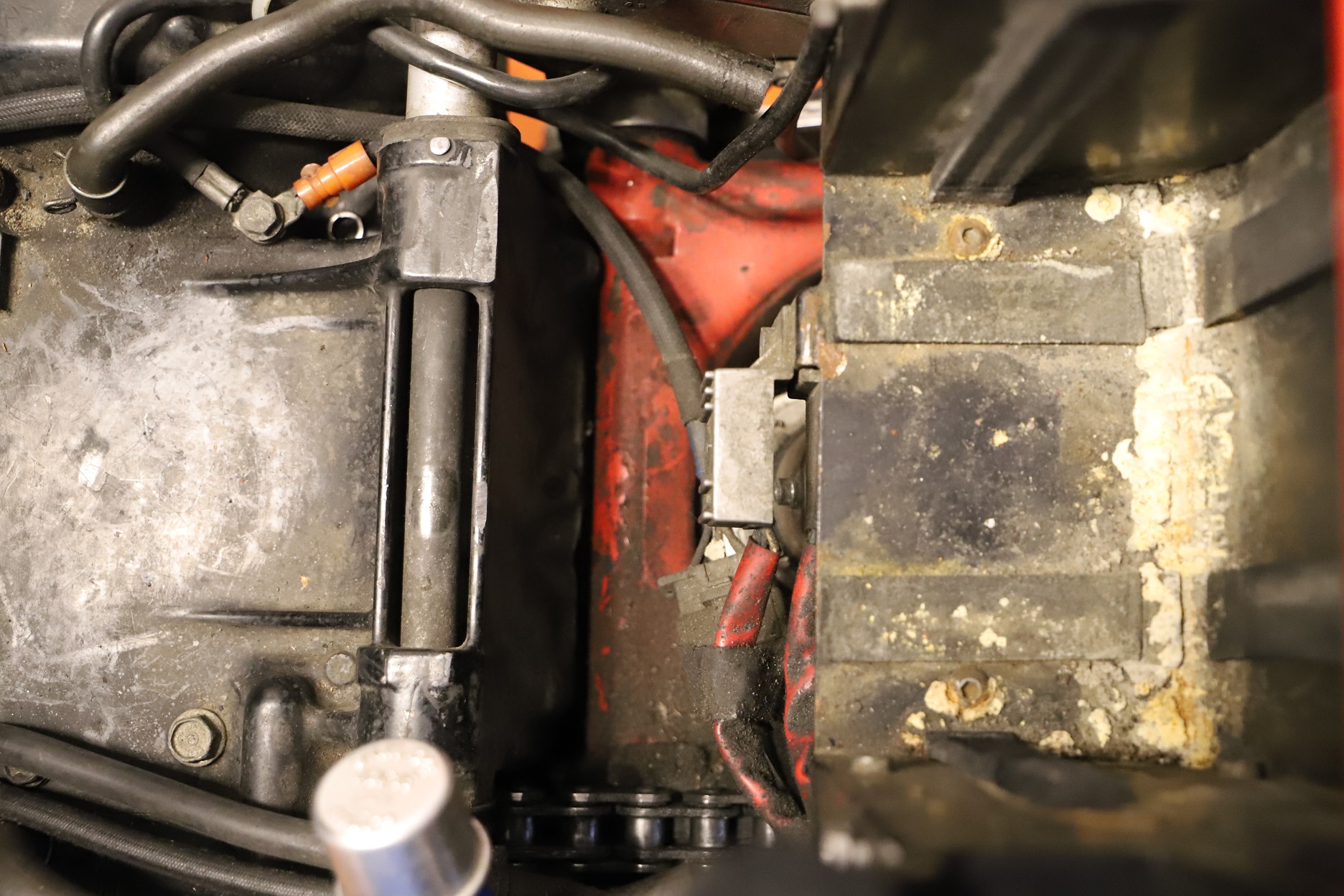
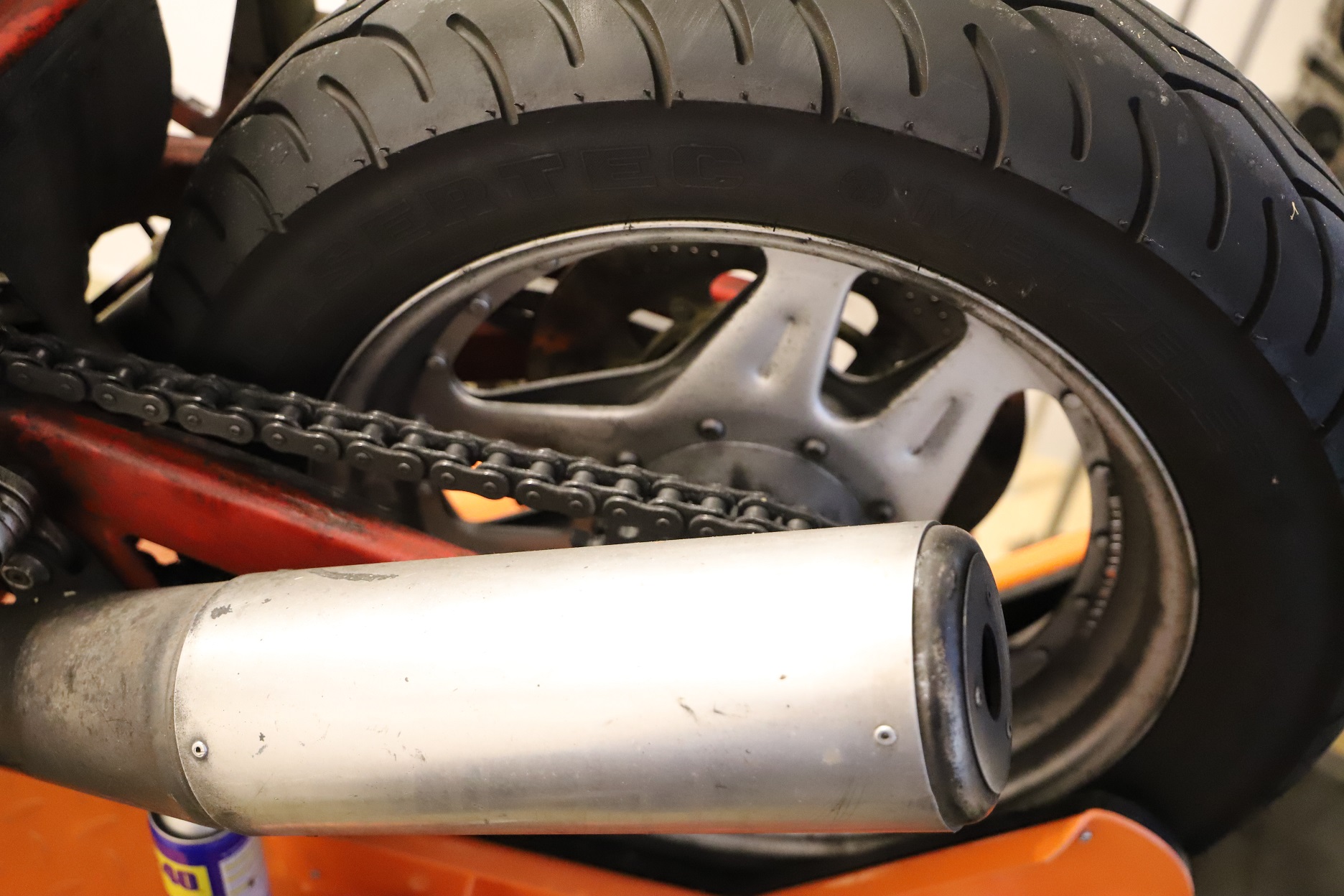
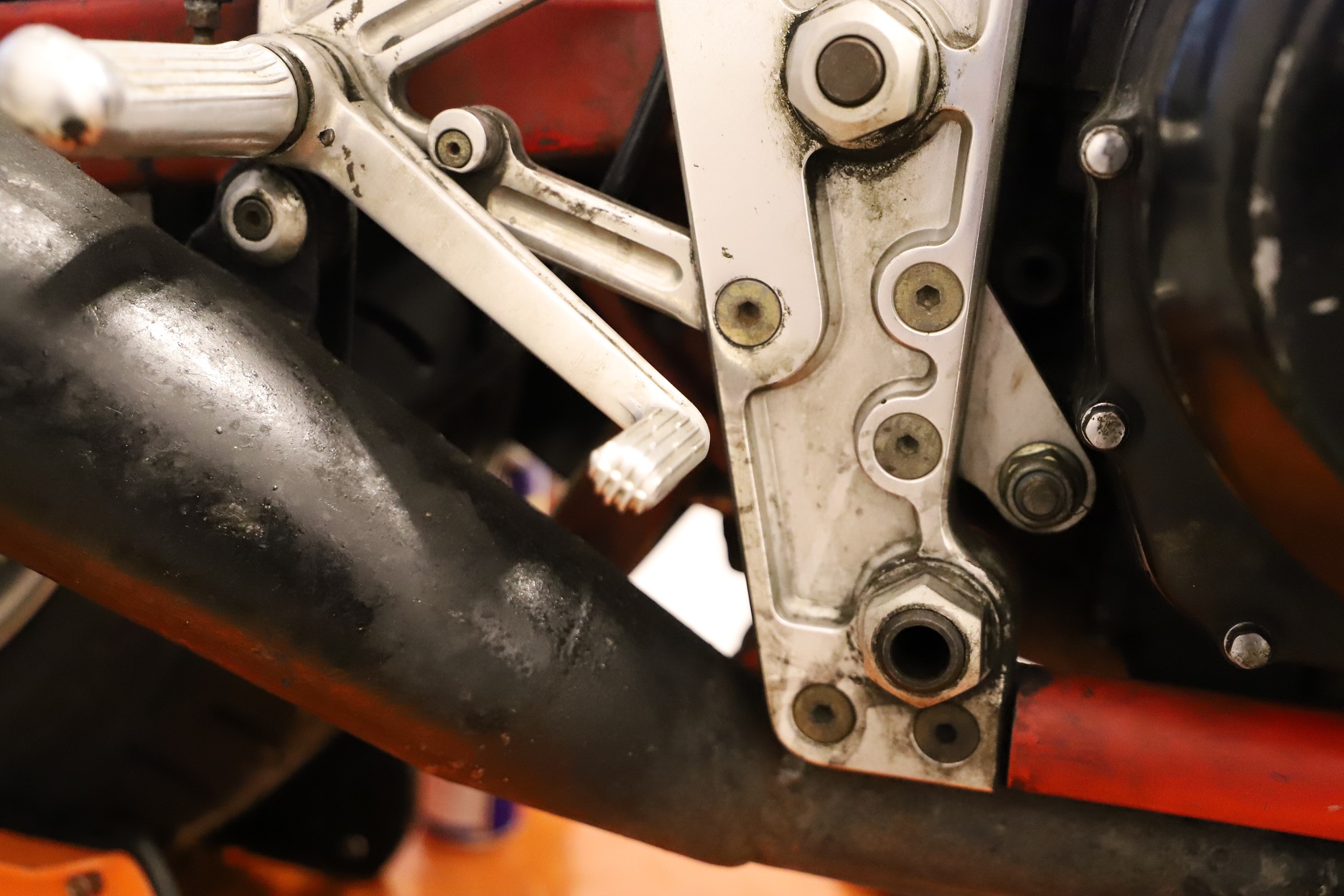
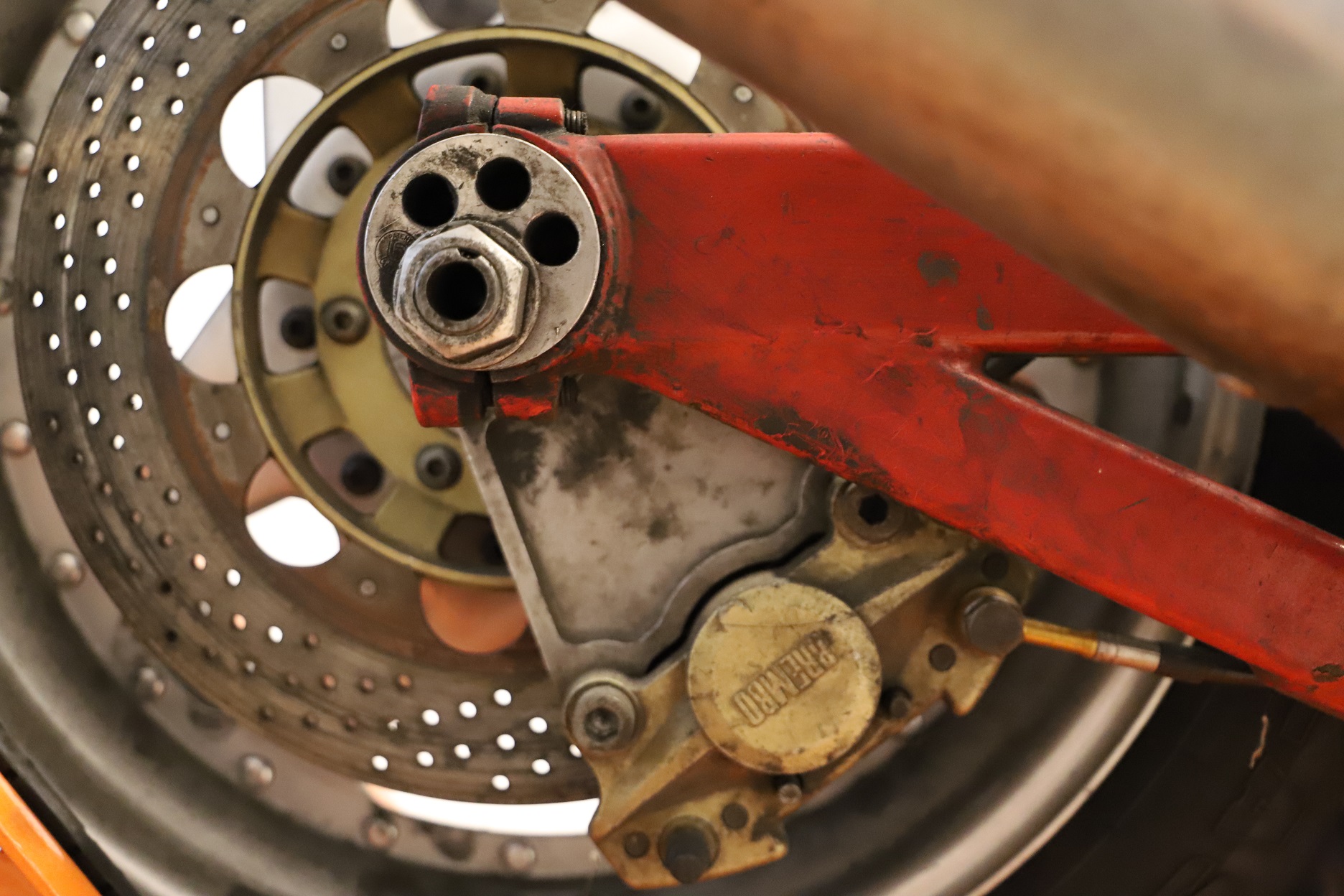
Alle lackierten Stahlteile (Rahmen, Schwinge, Halter usw.) müssen gestrahlt und anschließend neu pulverbeschichtet werden. Die Schrauben und Lager (außer vom Motor) werden komplett ersetzt. Die Aluteile sind in einem erstaunlich guten Zustand und lassen sich von Hand reinigen. Die Motordeckel werden poliert bzw. ebenfalls neu gepulvert. Der Kabelbaum ist zwar total verdreckt, aber nicht zerstückelt. Die alte Isolierung wird entfernt, beschädigte Kabel ersetzt und abschließend neu gewickelt.
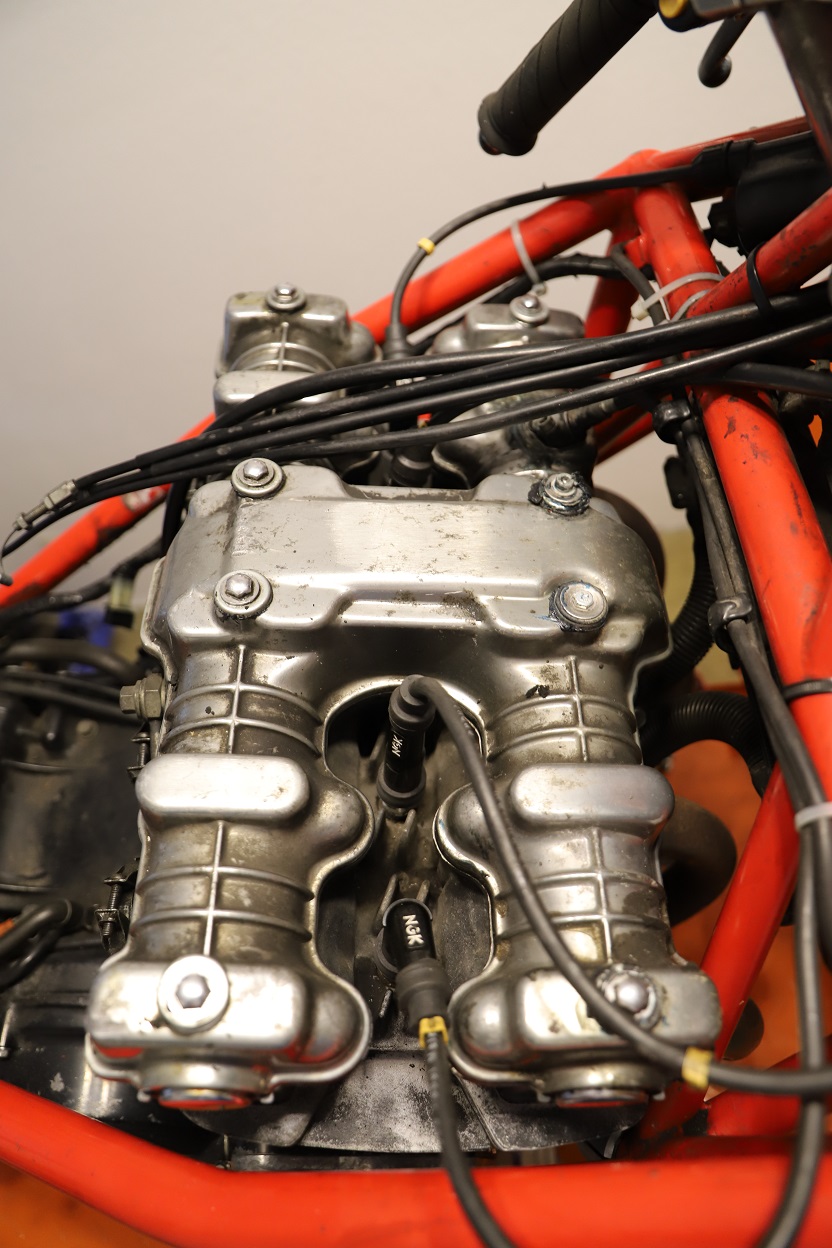
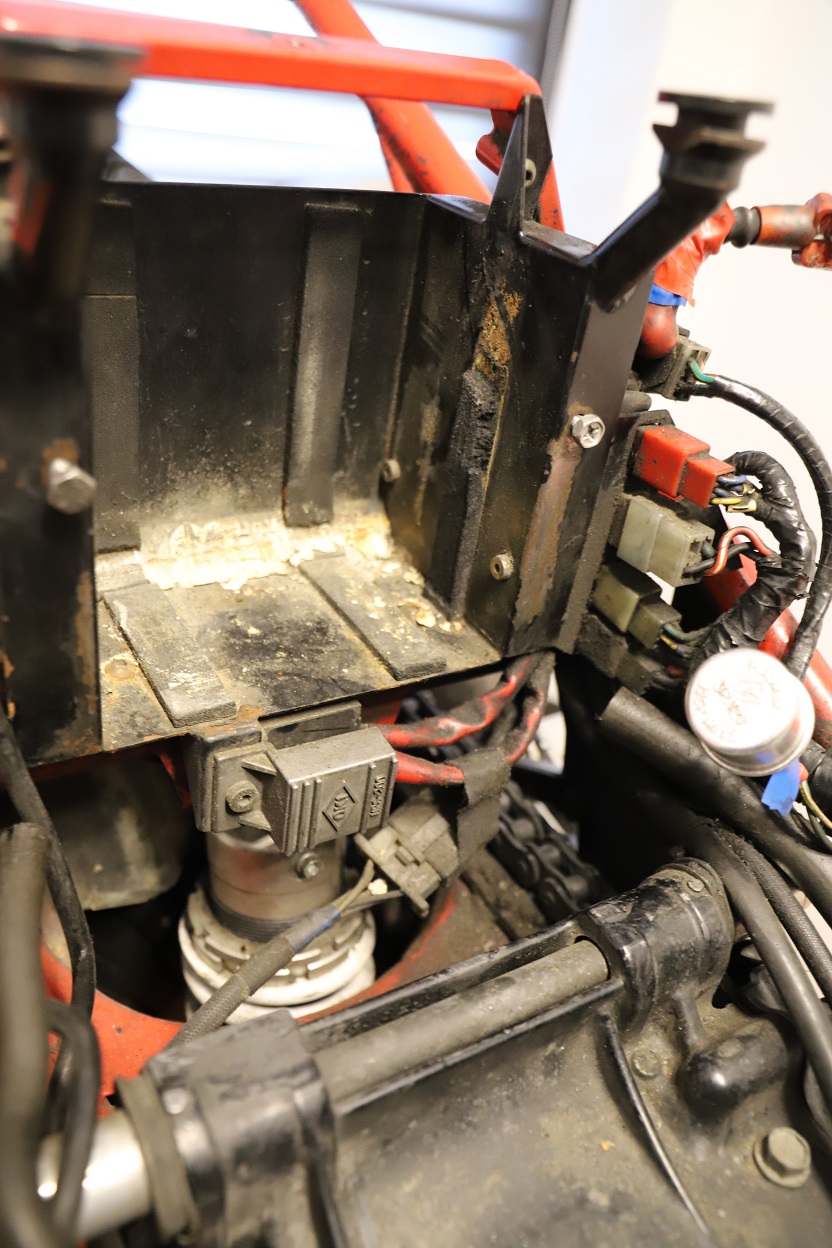
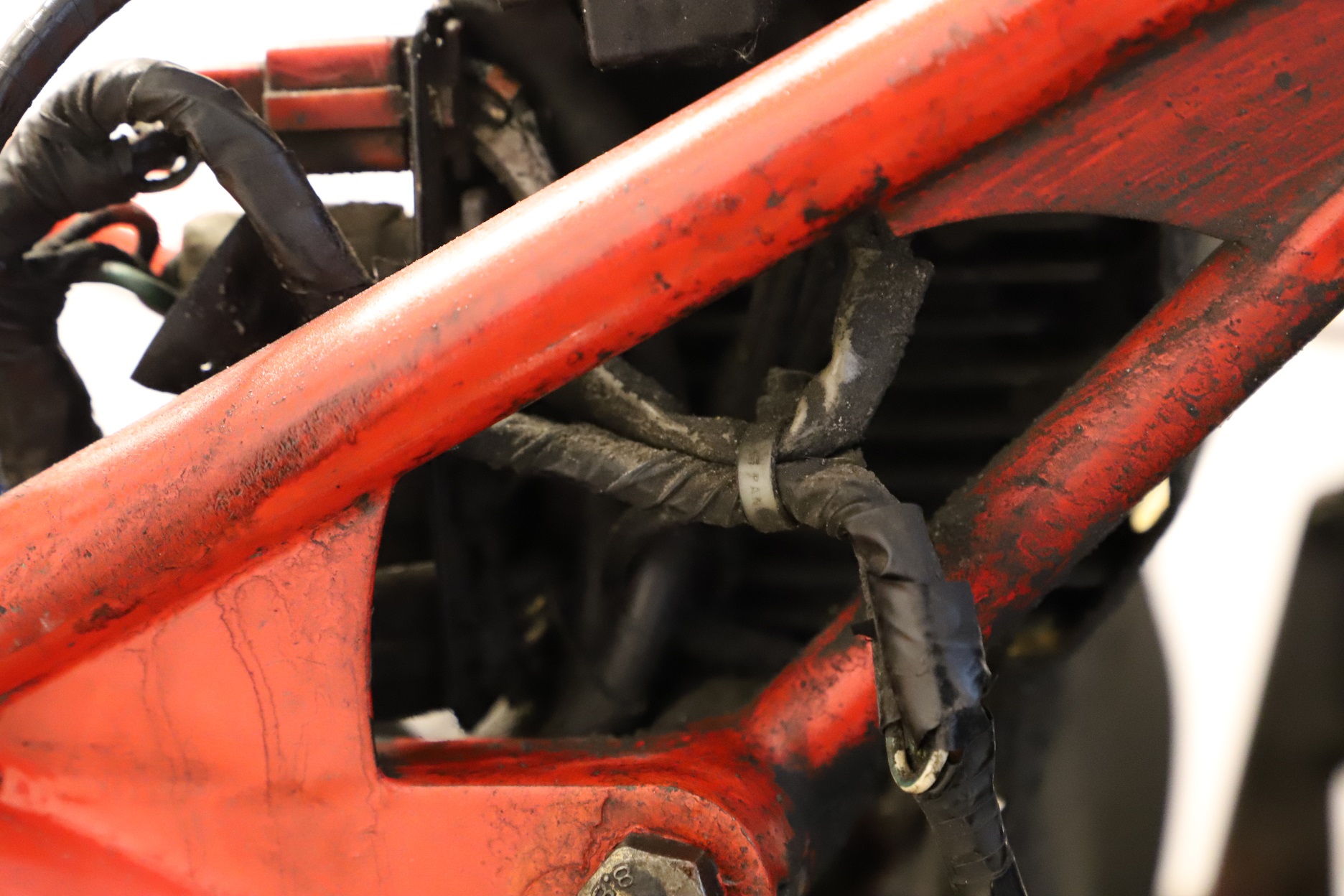
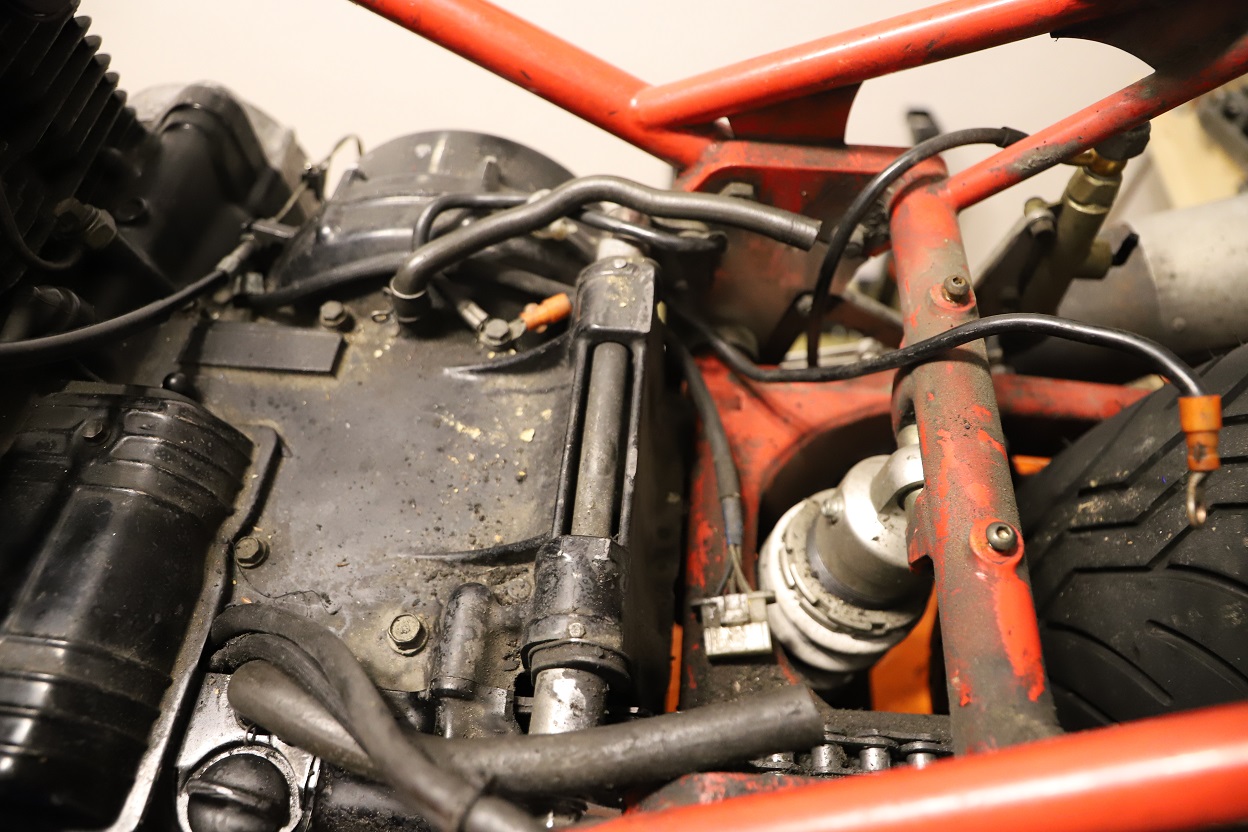
Bei der Demontage der Gabel fällt mir die De-Achsierung zwischen Lenkkopf und Standrohren auf. Schon seltsam. Ist das eine gewollte Einstellmöglichkeit des Nachlaufs, wofür dann aber eine andere Gabelbrücke erforderlich wäre, oder ein Work-Around eines Kleinserienherstellers, der nach der Fertigung von etlichen Rahmen feststellt, dass das Fahrverhalten des Motorrads für die Straße doch etwas zu extrem ist? Nein, natürlich nicht! Die nicht parallele Anordnung von Lenkkopf- und Gabelwinkel ist natürlich konstruktiv gewollt. Steht der Lenkkopf steiler als die Gabelstandrohre wird beim Eintauchen der Gabel die Reduzierung des Nachlaufs verringert.
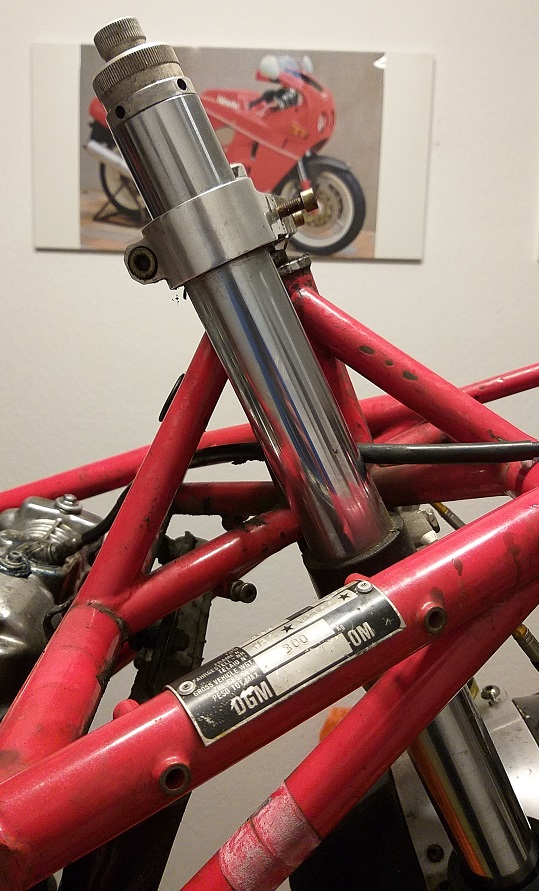
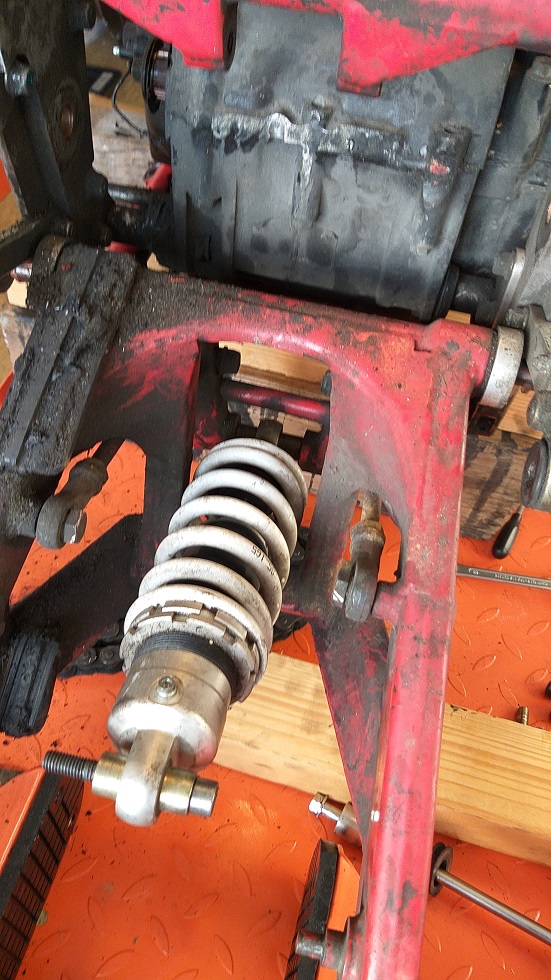
Nachdem alle aufzuarbeitenden Metallteile vorbereitet sind (Verschließen der Bohrungen, Gewinde und Lagersitze sowie Abkleben der bearbeiteten Passflächen), gehen die Teile Ende Januar zu einem Oberflächenspezialisten, werden mit Glasperlen gestrahlt und in den originalen Farbtönen neu pulverbeschichtet. Rahmenoberteil, Rahmenunterzug, Schwinge, Anlenkhebel für das Federbein und Koppelstangen in „Rosso traffico“ (RAL 3020 verkehrsrot) und Batteriekasten, Instrumententräger, Lampenringe, Hupenhalter, Schiene für Schmutzfänger, Scheinwerferhalter und Kupplungsdeckel in „Nero intenso“ (RAL 9005 tiefschwarz).
Parallel ist nun Zeit sich den Motor anzusehen, obwohl der laut Vorbesitzer völlig in Ordnung ist. Aber Vertrauen ist gut, Kontrolle ist besser. Also Kerzen raus und Kompression geprüft. Zylinder 2 und 4 haben nur 6,5 bar Kompression. Mit etwas Glück sitzen durch die lange Standzeit nur die Kolbenringe in den Nuten fest. Also WD40 in den Brennraum und erneut gemessen. Der Druck steigt sofort auf über 10 bar, fällt dann aber wieder ab. Erst nach einer mehrmaligen WD40 Kur haben alle Zylinder dauerhaft über 10 bar.
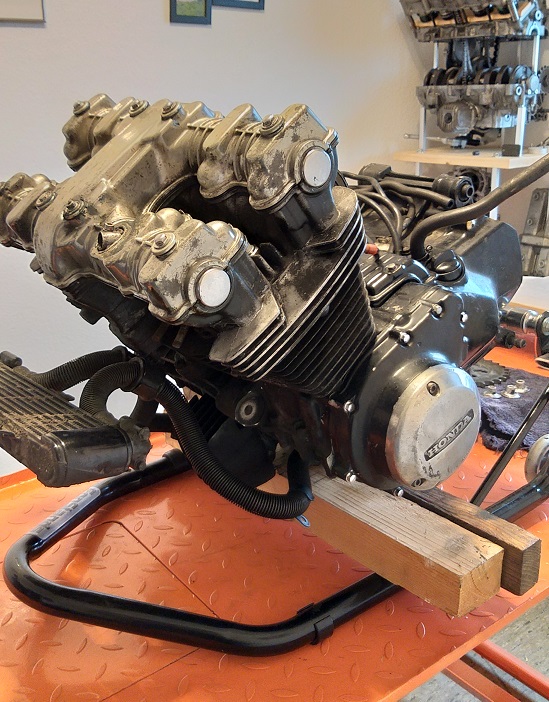
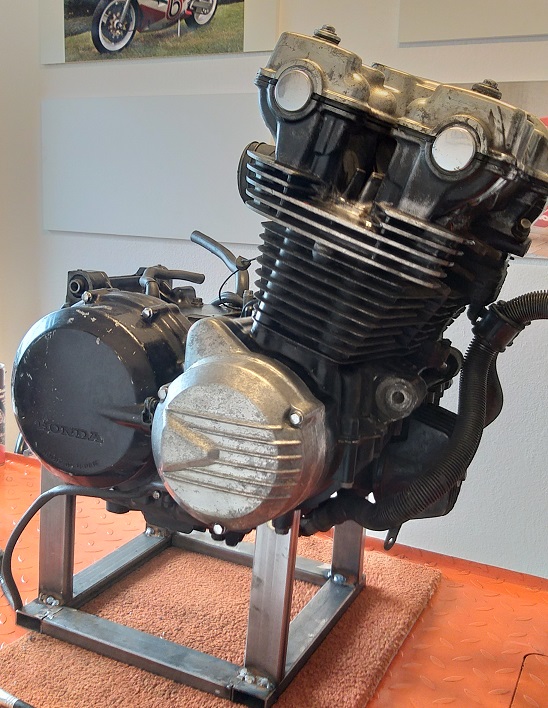
Dann Ventildeckel runter und das Ventilspiel kontrollieren. Das Sollspiel liegt bei 0,08 mm (max. 0,13, min 0,06) sowohl für die Ein- als auch die Auslassventil! Da hatte Honda die Wärmeausdehnung wohl im Griff. Das Spiel auf der Einlassseite ist i.o., aber auf der Auslassseite ist das Spiel auf 3 Zylindern deutlich zu groß. Egal, denn dies lässt sich bei diesem Motortyp mit Tassenstößeln und obenliegenden Shims einfach einstellen. Die Nocken sehen prima aus, so dass ich beschließe der Mechanik zu trauen und den Motor nicht weiter zu öffnen. Mit gereinigten und synchronisierten Vergasern und richtigem Ventilspiel sollte er wieder laufen.
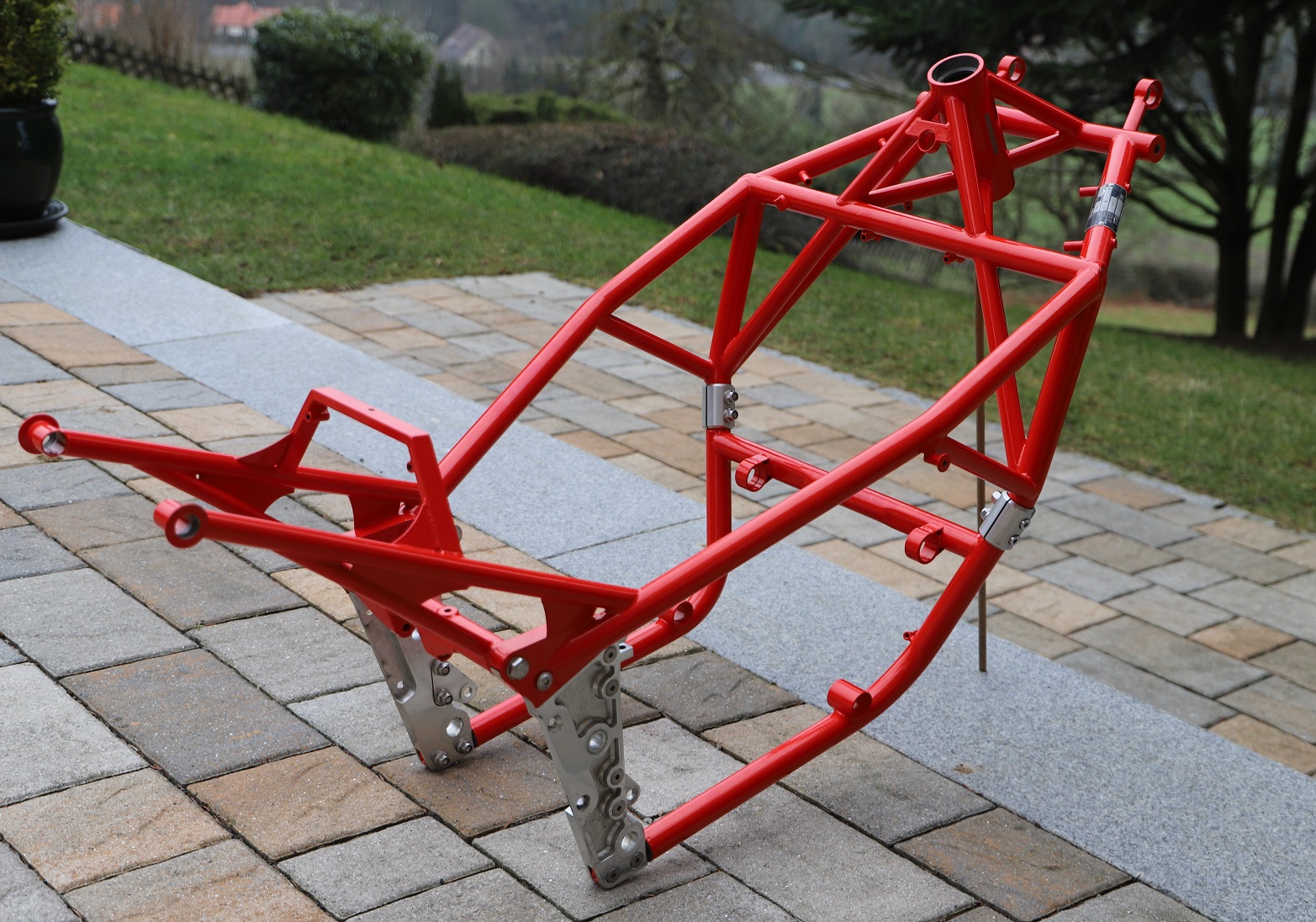
Wenige Tage später sind die gepulverten Teile fertig, sehen aus wie neu. Jetzt beginnt der schönere Teil der Restauration, der Zusammenbau bzw. Neuaufbau. Die Beschaffung der Neuteile ist teilweise einfach, teilweise ist Kreativität gefragt. Die verschiedenen Lager, wie z.B. die kombinierten Nadel-Rollenlager in der Schwinge, die Nadellager im Anlenkhebel des Federbeins oder die Kegelrollenlager im Lenkkopf sind noch den eingeprägten Teilenummern bestellbar und auch recht günstig.
Wesentlich zeitaufwendiger ist das Erfassen und die Bestellung der Schrauben, Muttern und Scheiben. Über 20 unterschiedliche Ausführungen allein für die Verschraubungen an Rahmen und Schwinge. Von M6 bis M10, von 12 bis 80 mm Länge, Innen- und Außensechskant, Senkkopf, Linsenkopf, flacher Kopf bis zu Voll- und Teilgewinde ist die Bandbreite der verwendeten Schrauben. Richtig spannend wird es bei den Motorlagern, da sie nicht gekennzeichnet sind und sich im Internet auch nach Stunden nicht finden lassen. Da die Suche mit Abmaßen auch nicht zum Ziel führt, suche ich nach den Maßen der Gummibuchsen. Am nächsten dran sind Stabibuchsen aus dem Mercedes Sprinter … .
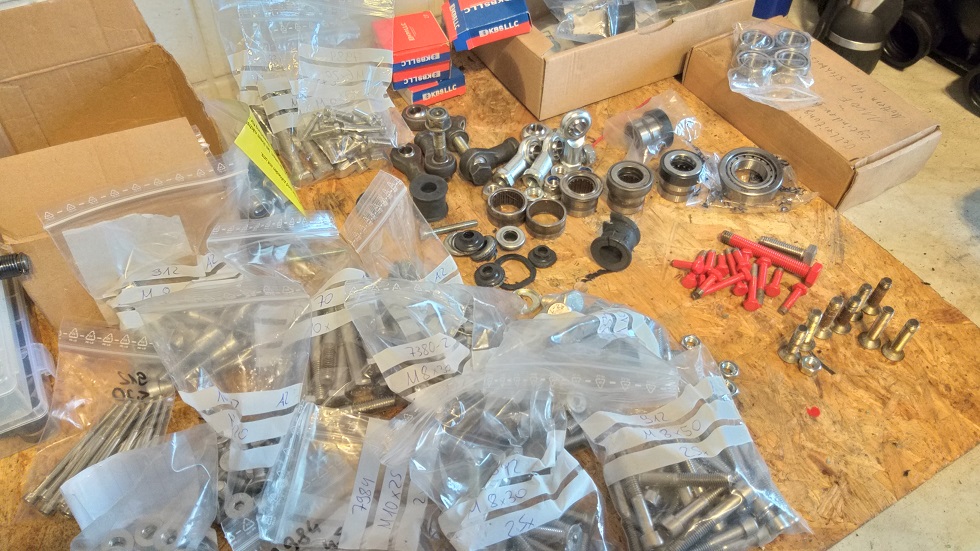
Fünf Tage später sind alle Lager eingepresst, Motor, Kabelbaum, Gabel, Schwinge, Räder und vieles mehr wieder verbaut. In den nächsten Tagen werden die sichtbaren Fortschritte kleiner. Arbeiten, wie z. B. das Befüllen und Entlüften der Bremsanlage, das Anfertigen von Kettengleitern aus einem Stück Delrin oder das Schweißen eines durchgerosteten Behälters der Kurbelgehäuseentlüftung, sind nicht mal eben gemacht. Aber Mitte Februar sieht der Aufbau so weit fortgeschritten, um erste Fotos unter freiem Himmel zu machen.
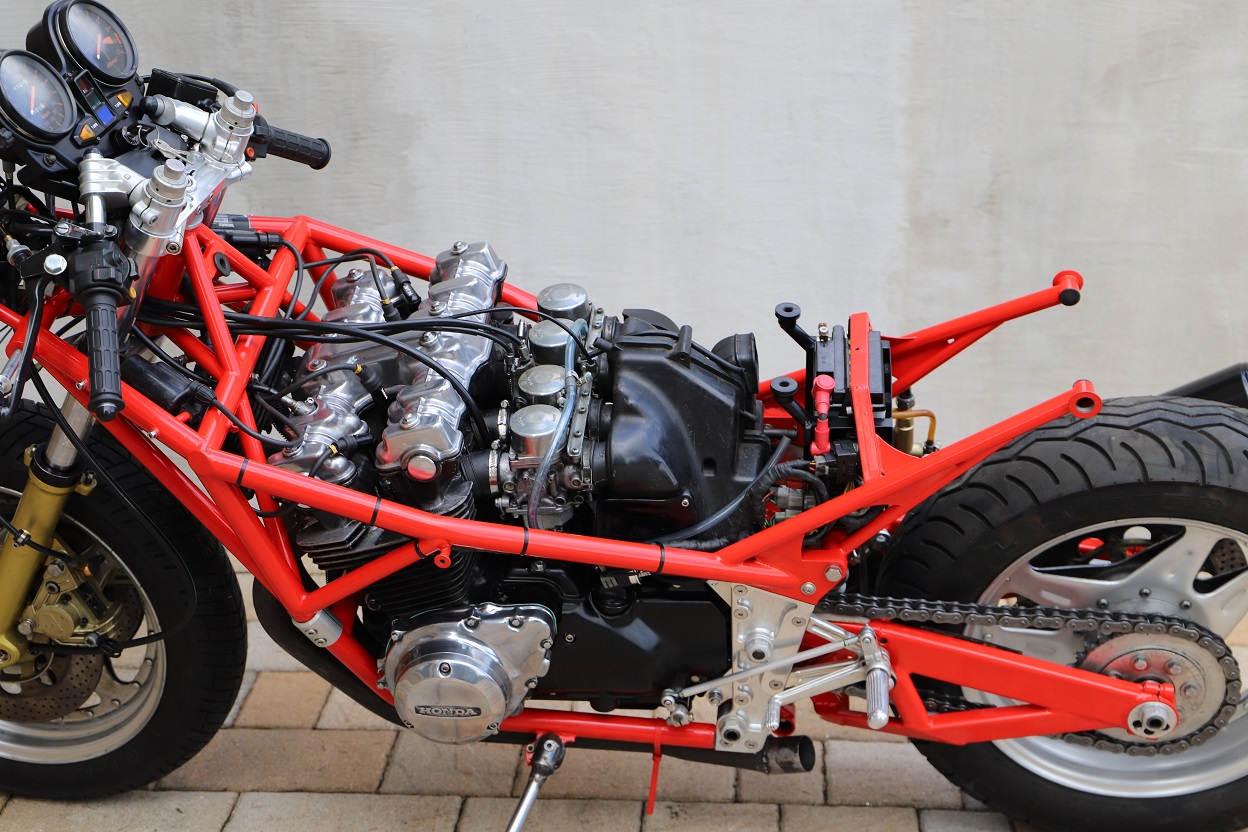
Am nächsten Tag ist die Verkleidung verbaut, um die Verlegung von Kabeln und Bremsleitungen zu prüfen. Dabei rückt ein altes Thema wieder in den Vordergrund. Der Vorbesitzer hat Verkleidung und Scheibe gekürzt, damit er mit einem hohen Lenker fahren konnte. Auf der Suche nach einer Lösung finde ich im Internet eine Firma, die Nachbauverkleidungen für SB4, HB2 und KB3 anbietet. Ich bestelle eine neue Verkleidung inklusive Scheibe, die nach knapp 6 Wochen fertig ist. Doch bei der Montage tauchen unerwartete Probleme auf.
Das kleinere Thema ist die Passgenauigkeit der Scheibe, die links deutlich tiefer über dem Scheinwerfer hängt als rechts. Das kann man anzeichnen und schleifen. Schlimmer ist, dass die Verkleidung nicht passt. Kupplungs- und Zündungsdeckel der Honda-Motoren liegen anders und sind größer als bei den Suzuki-Motoren der SB4. Außerdem sind die Ausschnitte für die Auspuffanlage bei der HB3 größer. Tja, wieder was gelernt; eine SB4 Verkleidung passt nicht an eine HB3. Ein Gutes hatte das Ganze. Zu der nicht passenden Scheibe wurde ich an den Hersteller, die Firma Polybauer, verwiesen.
Ende April fahre ich mit meinen Teilen nach Lehrte und lerne Dietrich Polybauer kennen, der in den späten 1970er und 1980er Jahren als Verkleidungsbauer in aller Munde ist. Inzwischen ist er im Ruhestand und seine Söhne führen das Unternehmen, haben den Schwerpunkt aber Richtung Reifenhandel und PKW Tuning verschoben. Dietrich hat sich meine abgesägte Verkleidung angesehen, sich ihrer angenommen, in der Formenwerkstatt ein Modell bauen lassen und die fehlenden Enden der Verkleidung nachmodelliert. Am 3. Mai ist die Verkleidung fertig. Klasse Arbeit zum fairen Preis!
Das Thema Abgasanlage kostet richtig Zeit und Nerven, da keine originalen Teile zu bekommen sind. Um weiterzukommen kaufe ich über ebay Kleinanzeigen zwei gebrauchte Zubehör-Enddtöpfe einer CB1100 bei einem Honda Sammler in Wadersloh. Die Endtöpfe sind von Fa. JAMA aus Holland und haben eine ECE-Zulassung, erkennbar am Symbol e4 im Rechteck. Die Firma ist allerdings seit 2012 pleite, weshalb es schwierig werden dürfte, die passenden Unterlagen zu finden. Bis zur Abnahme findet sich sicher eine Lösung. Erst einmal müssen sie angepasst werden.
Die Flex zum Abrennen der alten Schalldämpfer habe ich schon in der Hand als mir auffällt, dass hier schon mal jemand Hand angelegt hat. Die rechte und linke Seite sind nicht symmetrisch und im Übergang Krümmer zum Endtopf wurde geschweißt. Also wird das nichts mit einfach abschneiden und Neue aufschieben. Aus Kanthölzern baue ich mir eine Vorrichtung, um die Schalldämpfer symmetrisch ausrichten zu können. Mit Bögen und Muffen aus dem Zubehör für PKW Abgasanlagen verbringe ich ganze Tage mit ausrichten, heften, montieren, passt nicht, trennen, wieder ausrichten usw, „Final“ alles verschweißen und Schweißnähte polieren. Dann nur noch schnell Halter aus Flachstahl biegen und schweißen und schon sollte alles passen. Bis ich dann bei der Montage feststelle, dass die Halter doch zu dicht an der Schwinge sitzen und alles noch einmal um ein paar Grad korrigiert werden muss …
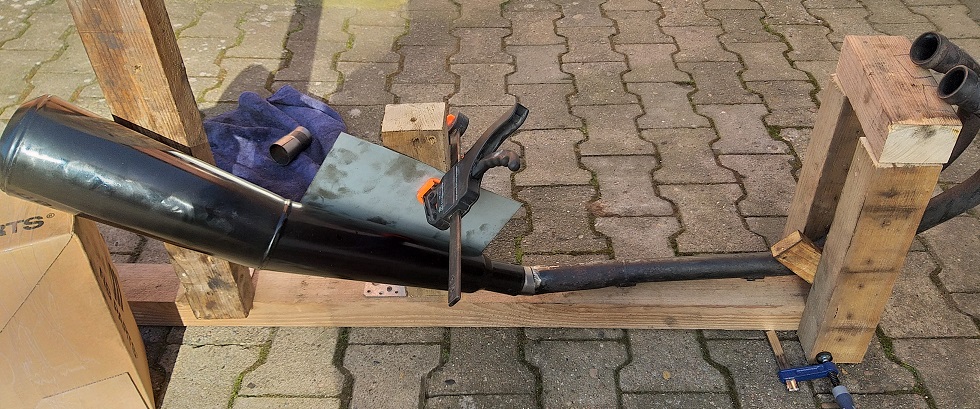
Aber irgendwann ist auch die Abgasanlage fertig und damit der Zeitpunkt gekommen, um den Motor wieder zum Leben zu erwecken. Mit einer großen PKW Batterie, Überbrückungskabel und separatem „Kraftstoffbehälter“ geht das erstaunlich reibungslos. Wie erwartet klappern die Auslassventile und der Motor läuft nicht richtig rund. Trotzdem freue ich mich und teile meine Freude mit einem kurzen Video im WhatsApp Status. Darauf meldet sich mein Bimota-Freund Harald, der das Video gesehen und vor allem gehört hat und fragt, ob ich eventuell das Werkzeug zum Tauschen der Ventilplättchen und einen Synchrontester brauchen könnte :-).
Nachdem alles eingestellt ist, schnurrt der 1100er wie es sich gehört. Nach knapp 3 Monaten ist das Gros der Restauration erledigt. An Restarbeiten bleibt die Lackierung, die Kettenradaufnahme der hinteren Felge und Kleinigkeiten wie Blinker, Sitzbankpolster und Hitzeschutzfolie für die Verkleidung. Ich bestelle noch die Aufkleber für die Lackierung, die ich bei einer Werbeagentur anfertigen lasse, und suche weiter nach einer Felge, da es nicht ohne geht. Aber jetzt ist Frühling, die Saison geht los und die Fertigstellung muss warten bis der nächste Winter kommt.
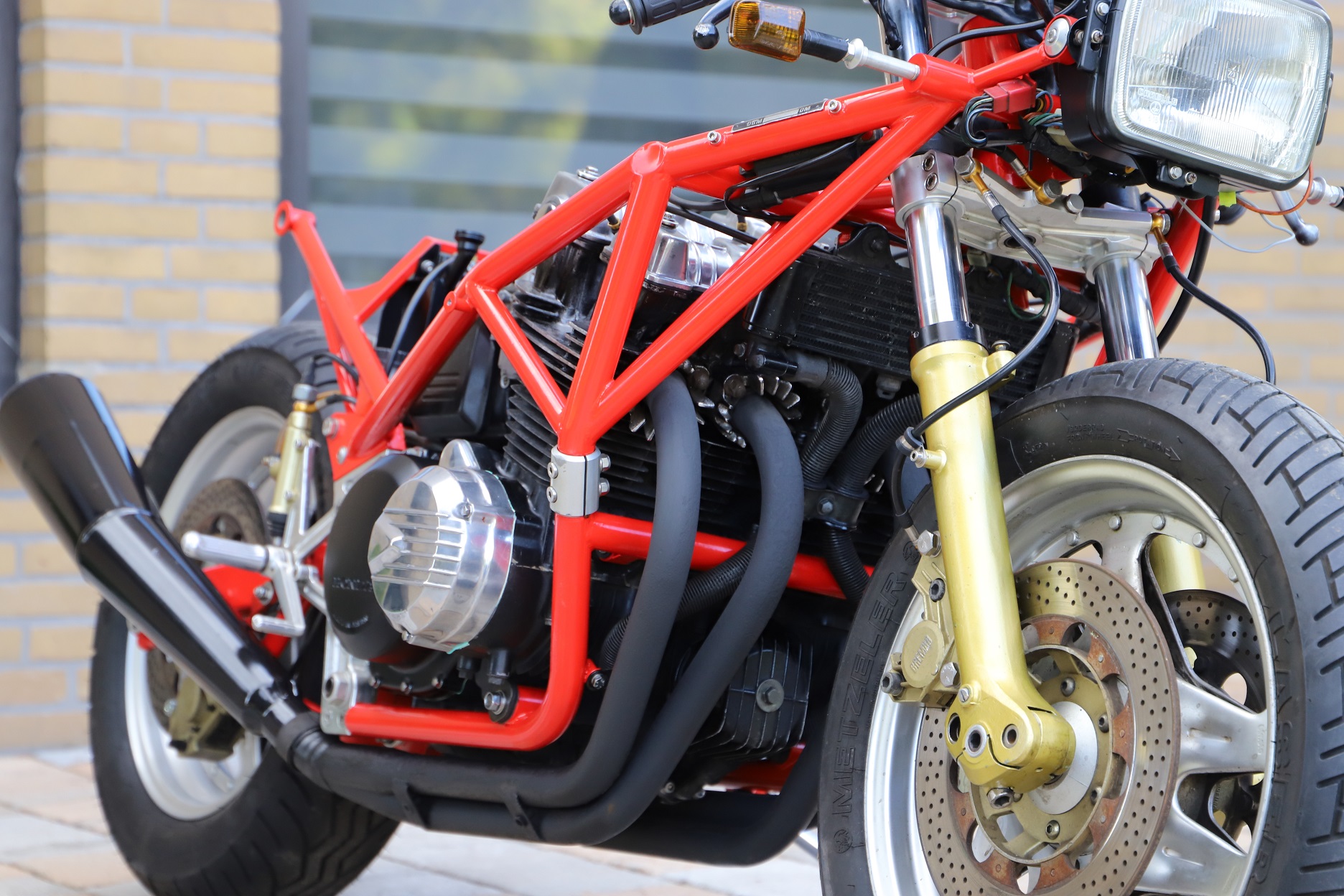
Es wird dann doch Frühjahr 2022 bis ich weitermache. Die Herstellung des Sitzpolster aus einer 20 mm Zellkautschukmatte ist einfacher als gedacht. Das Material lässt sich einfach schneiden und schleifen. Honda Blinker aus den 80er Jahren finde ich bei ebay. Bleiben Felge und Lackierung.
Ach ja, die Hinterradfelge. Bereits am 15.01.2001 mache ich beim Zerlegen eine unerfreuliche und unglaubliche Entdeckung, für die ich erst ein Jahr später eine Lösung habe. Das Ritzel und die Kettenradaufnahme sind durch verschlissene Ruckdämpfer und/oder falsche Teile komplett verschlissen. Ich frage mich immer noch wie man so etwas montieren kann bzw. wie man das bei Fahren nicht bemerkt.
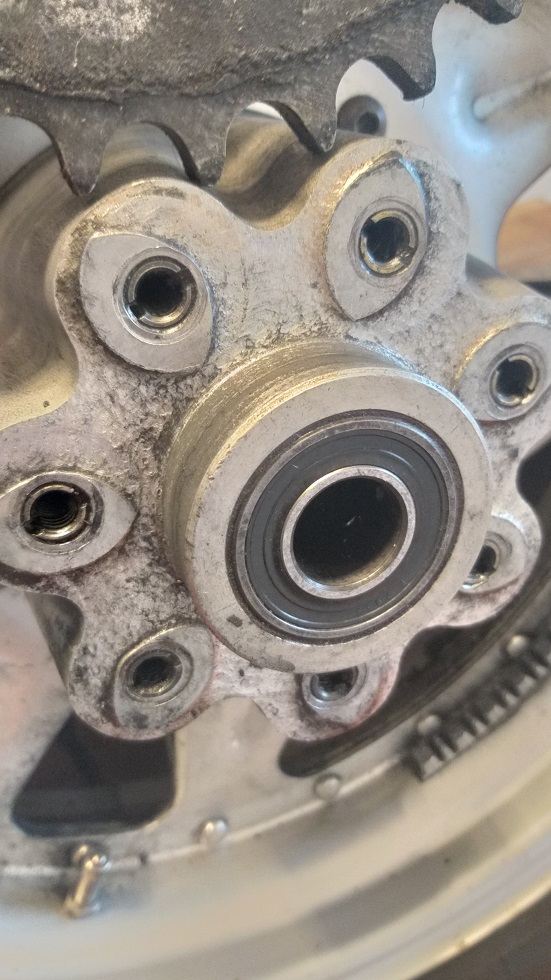
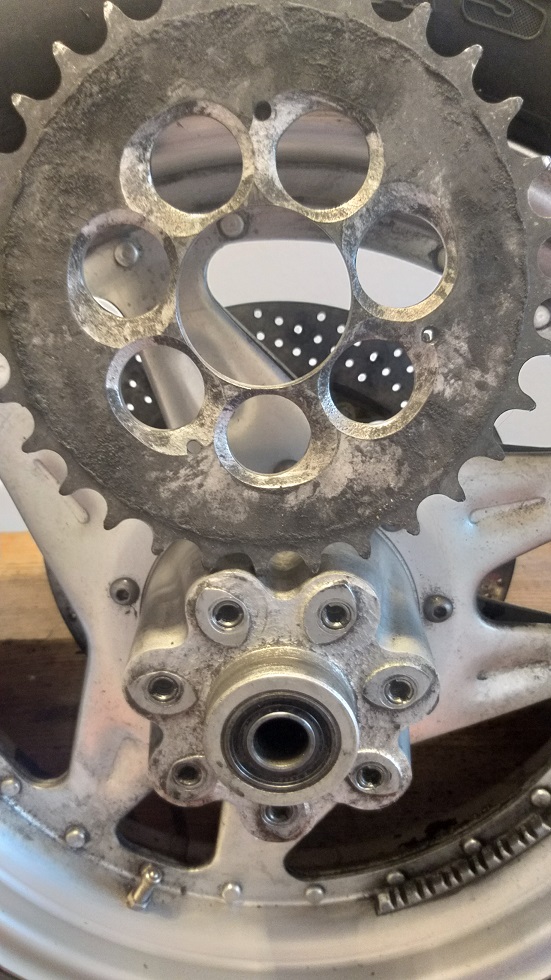
Ende Januar 2022 wird glücklicherweise eine weiß lackierte Felge auf ebay Kleinanzeigen angeboten, die ich bei einer auf Felgenaufbereitung spezialisierten Firma im Laugenbad entlacken lasse. Dabei hat sich das Dichtband im Bett der genieteten Felge zersetzt. Bimota rühmte sich in den 1980er Jahren dafür, eine gebaute Felge mit Hightech Teflonband aus der Raumfahrt abgedichtet zu haben und somit schlauchlose Reifen fahren zu können. Heute reicht eine herkömmliche Kartusche Felgendichtmittel, um das Problem zu lösen. Da Bimota die Felgen serienmäßig eloxierte, war nach dem Entlacken keine weitere Oberflächenbehandlung erforderlich.
Die letzte Herausforderung ist die Lackierung. Die HB3 wurde in vier verschiedenen Lackierung angeboten. Von den 101 ausgelieferten Maschinen trugen 29 das klassische rot/weiß, 24 die Farbenkombination rot/weiß/blau der Honda Racing Corporation HRC, 46 das Design in rot/weiß/grün und 2 wurde komplett grau lackiert.
Um festzustellen, in welcher Lackierung diese HB3 ausgeliefert wurde, habe ich Verkleidung und Monocoque angeschliffen. Erfreulicherweise kam die aufwendigste und für mich schönste Farbkombination in rot mit weißen Flächen und grünem Streifen zum Vorschein.
Damit ist auch klar, dass meine SB4 S wunderbar als Muster für die Lackierarbeiten dienen kann, da sie bis auf den grünen Streifen das inverse Farbschema trägt.
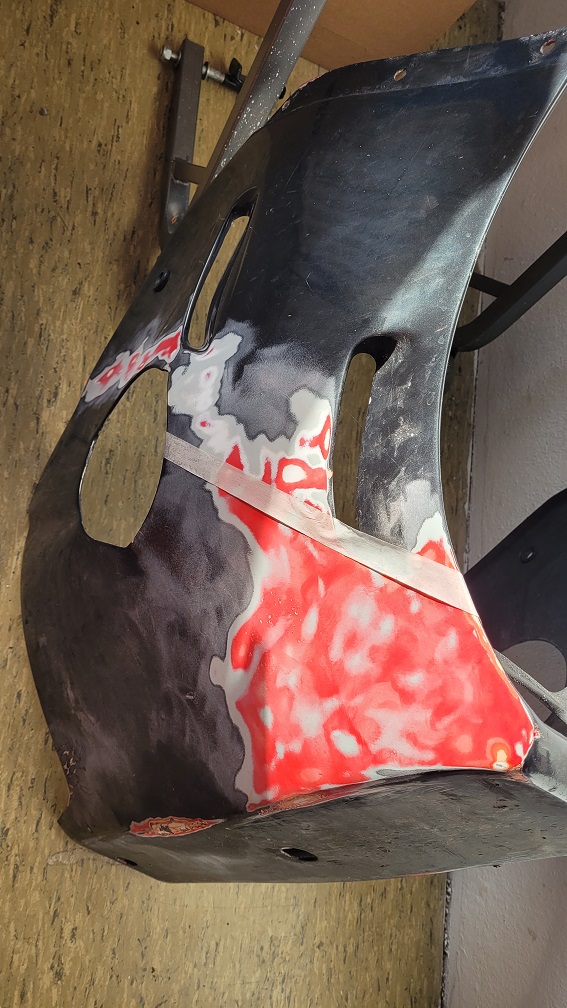
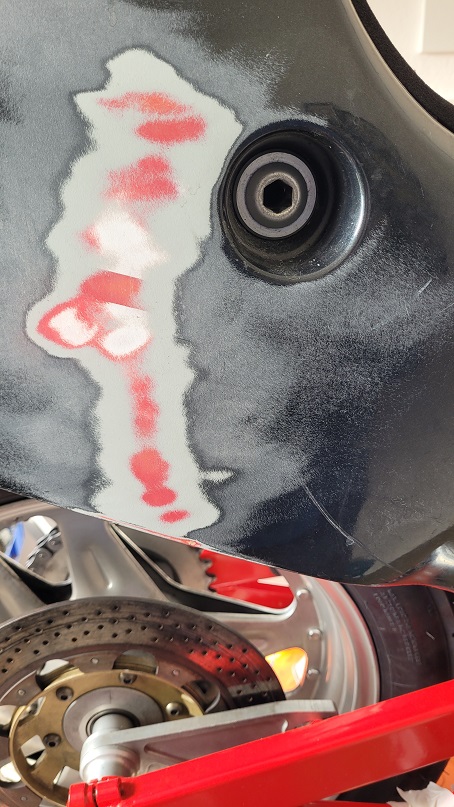
Bei der Lackierung habe ich mich für Fa. Rauhut in Rehren entschieden, da sie bereits bei einer vorherigen Restaurierung super Arbeit abgeliefert haben. Mit den Teilen war ich in 2021 schon mal da um zu klären, ob sie die vielen Risse und Löcher in der Verkleidung reparieren und beseitigen können.
Als ich dann am Ende April mit meiner zweiteiligen Verkleidung, Monococque, Schutzblech und Staufachabdeckung und vielen Fotos aus dem Internet zur gewünschten Lackierung wiederkomme, muss ich den Juniorchef doch ziemlich für den Job motivieren. Der Zustand der Verkleidung, das aufwendige Farbschema mit 4 Farben und die Herausforderung des Abklebens der weißen Flächen sind keine alltägliche Aufgabe. Ich biete meine SB4 als Muster an und erstelle eine Liste mit der Position aller Aufkleber und Flächen.
Fast 4 Monate später, am 15. August, ist es dann vollbracht. Die Teile sind fertig, sehen top aus und ich bin Felix Rauhut wirklich dankbar, dass er sich die Zeit genommen hat, um es vernünftig zu machen.
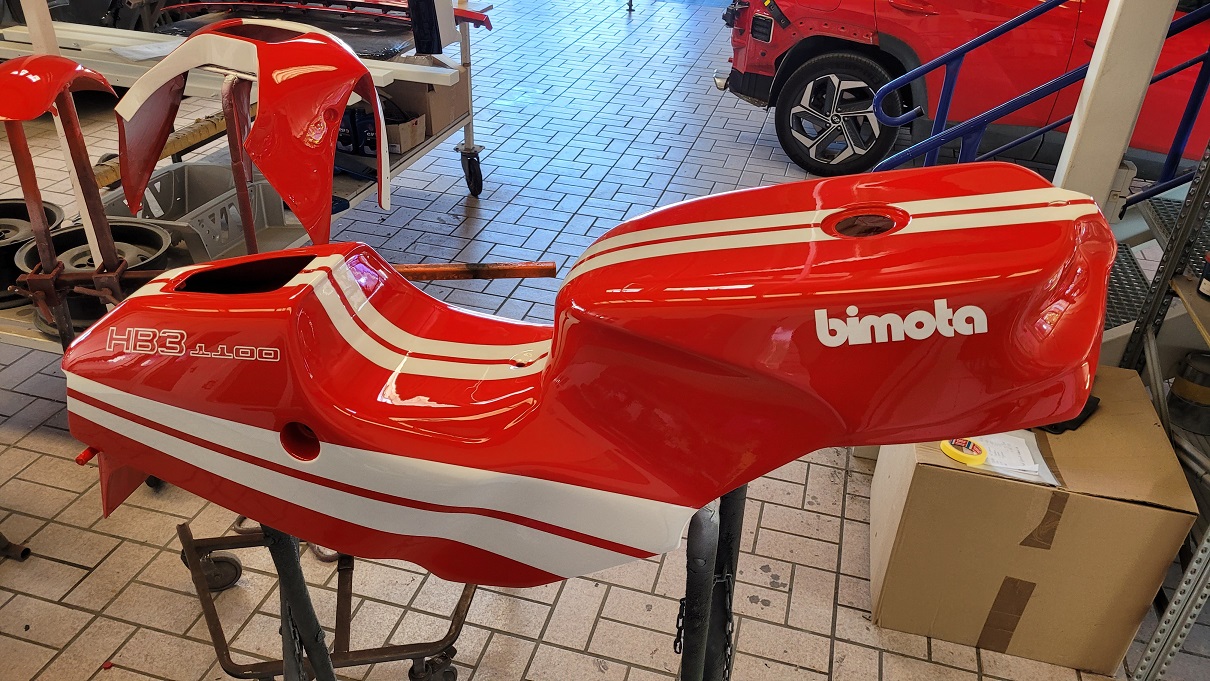
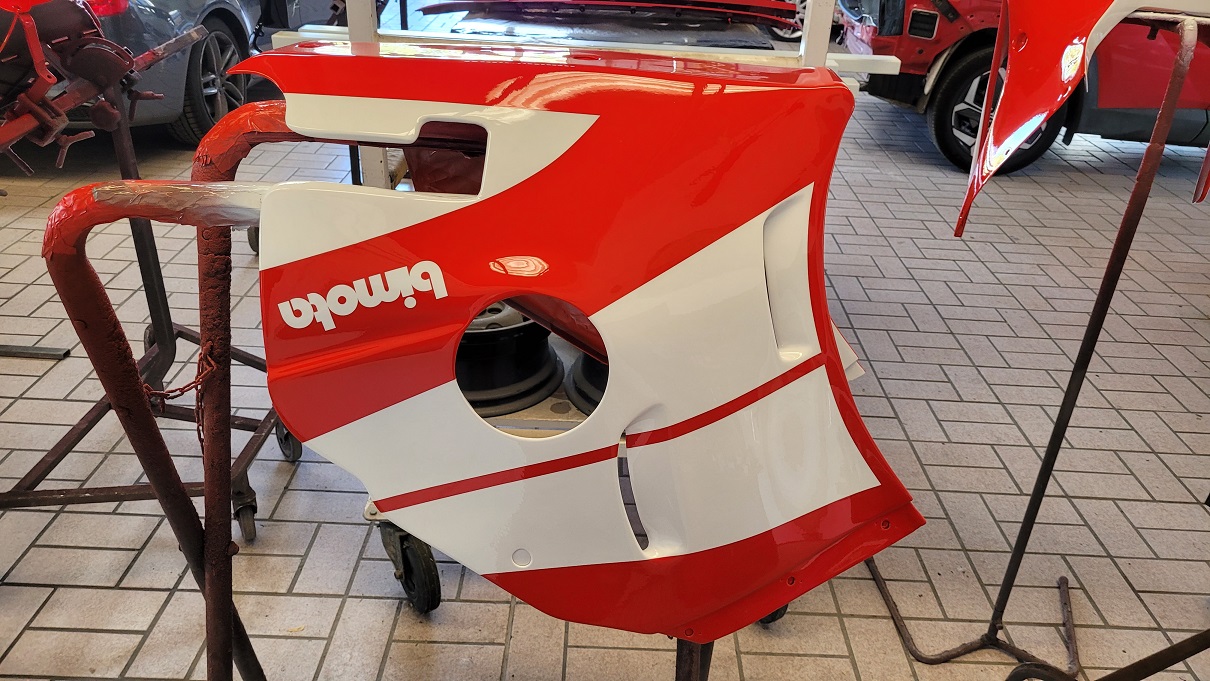
Im September 2022 wird es noch einmal spannend. Ich habe einen Termin beim TÜV in Hameln gemacht, um die Abgasanlage eintragen zu lassen. Im Vorfeld hatte ich dazu mehrfach telefoniert und Informationen per Mail verschickt. Offiziell heißt das „Begutachtung nach §21 StVZO nach Erlöschen der Betriebserlaubnis“. In der Praxis heißt das Einzelabnahme mit Probefahrt, Begutachtung und Geräuschmessung bei halber Nenndrehzahl sowie einem Gesamtbetrag von 151,80 Euro.
Der Prüfer ist mit meinem Eigenbau einverstanden und von der HB3 merklich angetan. Er bietet an die im Juli 2018 abgelaufene Hauptuntersuchung sowie die „Begutachtung für die Einstufung als Oldtimer nach §23 StVZO“ ebenfalls durchzuführen. Das hatte ich zwar nicht geplant aber die Gelegenheit scheint günstig. Weitere 43,20 Euro für eine Hauptuntersuchung „ohne erkennbare Mängel“ und 69,02 Euro für das Oldtimergutachten werden fällig. Damit sind alle Voraussetzungen für die Zulassung auf mein neues 07er Kennzeichen erfüllt und das Projekt Wiederbelebung der HB3 abgeschlossen.
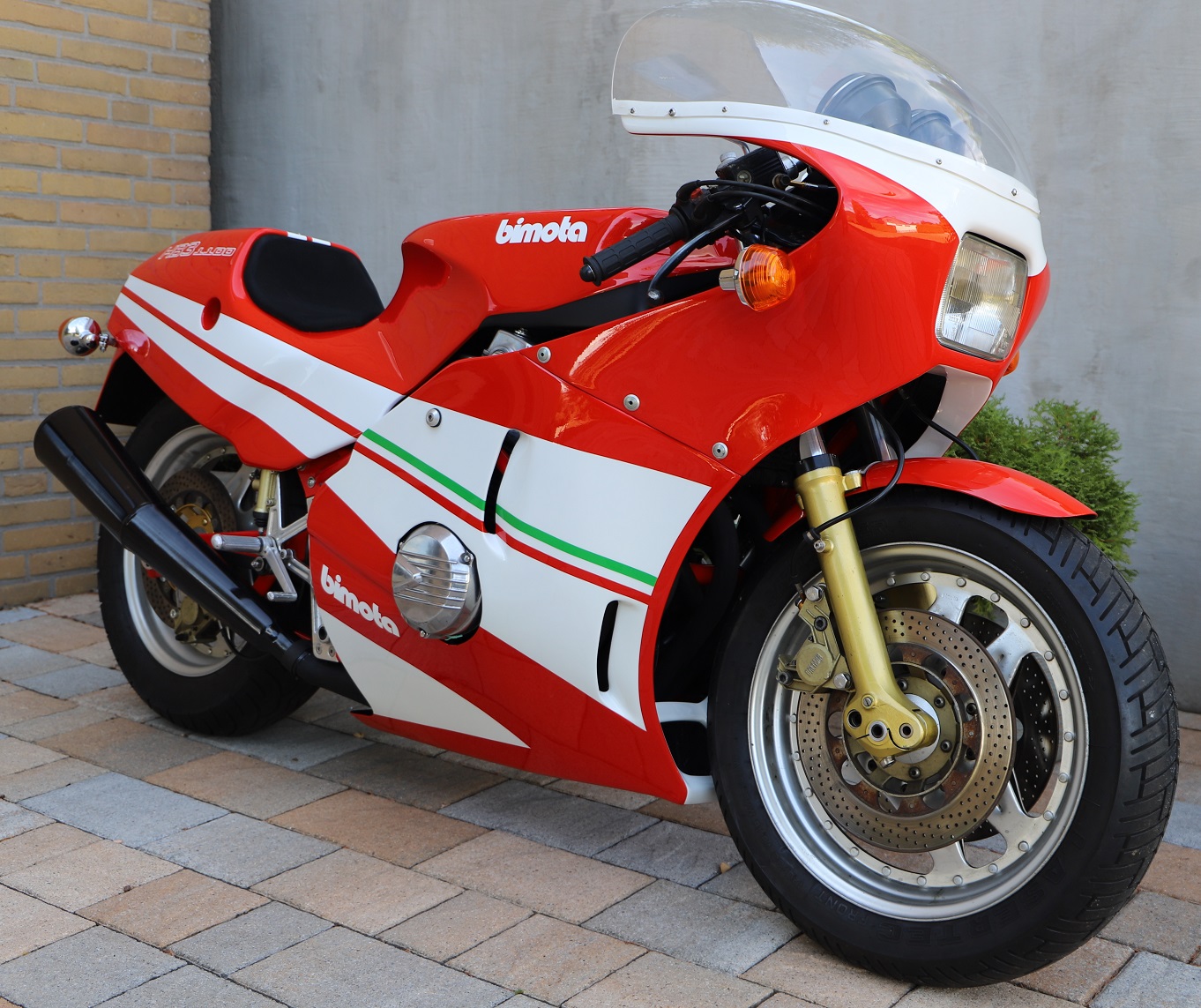